01
穴あけDrilling
基板材料に高回転させたドリルで指定座標に貫通穴をあける工程。ドリル径は最小φ0.06から最大φ4.0mm、ドリル回転数は最大30万回転/1分間
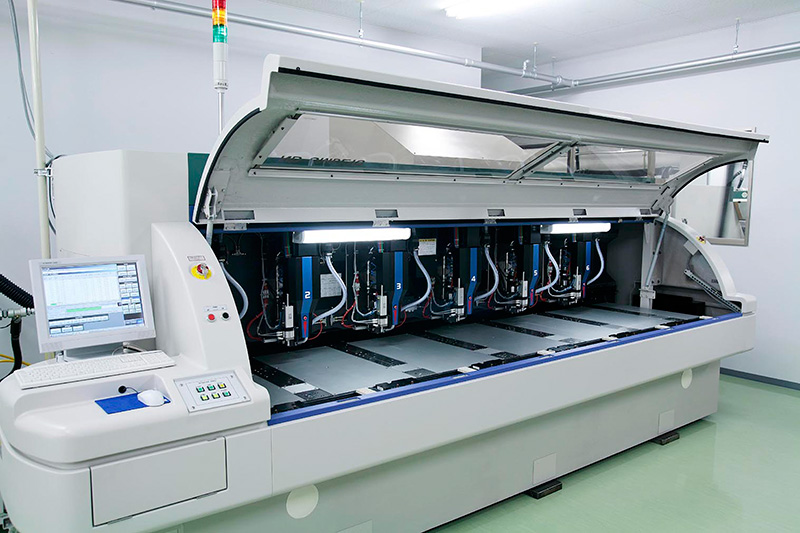
02
銅めっきCopper plating
基板表面と貫通穴側面へ銅めっきを施し基板表裏の導通性を確保させる。めっき厚みは製品種ごと異なるが最小8μmから最大30μm程度。
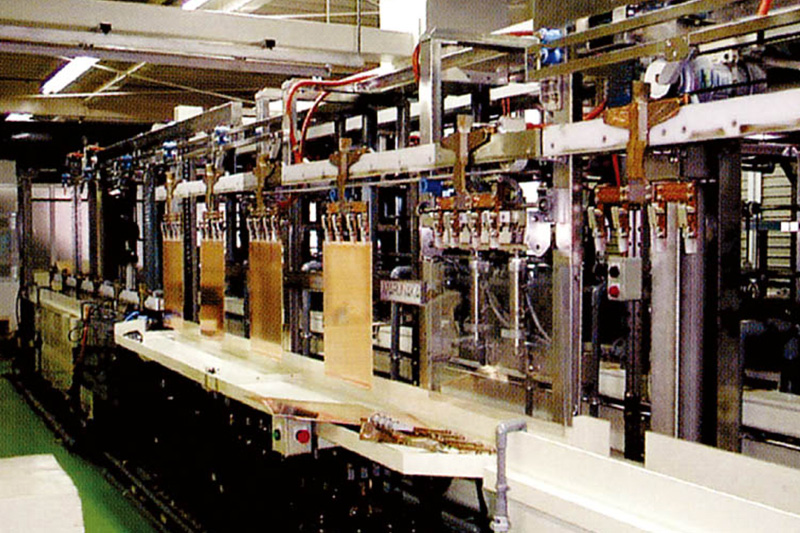
03
ラミネート(回路形成)
Laminate
配線を形成するために基板表面へ感光性フィルムを貼り付ける工程。フィルム厚さは製品種ごと異なるが最小10μmから最大50μm程度。
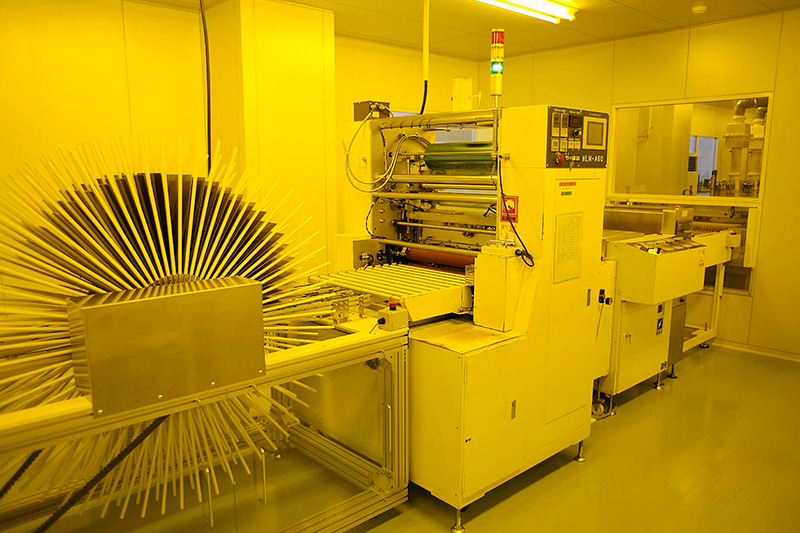
04
露光(回路形成)Exposure
専用フィルムを用いて配線となる箇所へ紫外線を照射、配線とならない箇所へは遮光し照射させない工程。
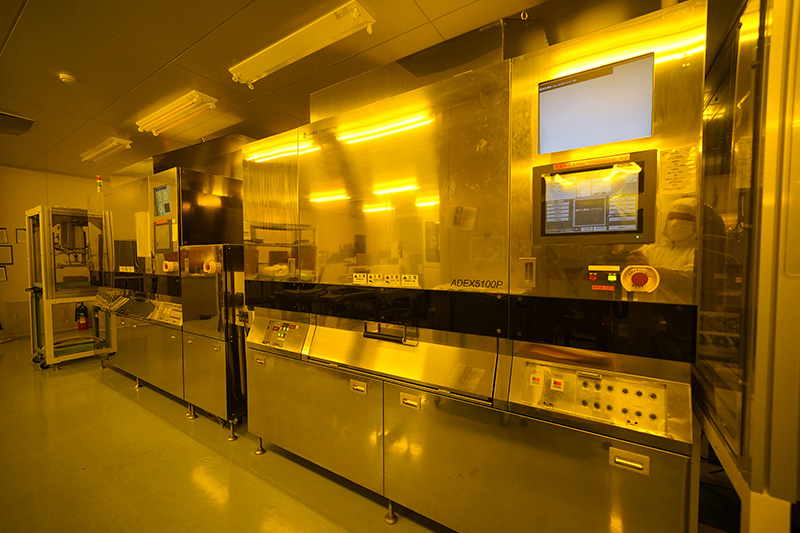
05
現像(回路形成)Developing
アルカリ性の専用薬液によって配線とならない箇所の感光性フィルムを溶解(除去)する工程。
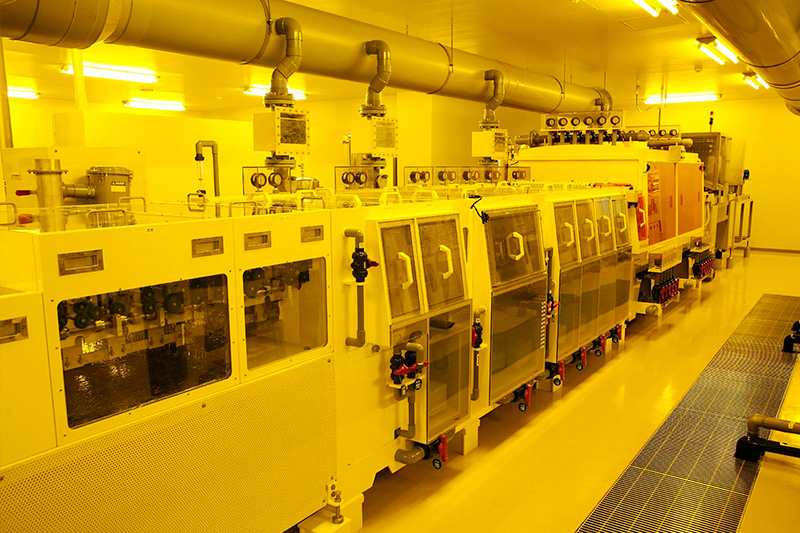
06
エッチング・剥離
(回路形成)
Etching / Peeling
不要な箇所の銅を溶かし配線を形成する。最終化学反応は以下の通りFeCl3 + CuCl →FeCl2 + CuCl2
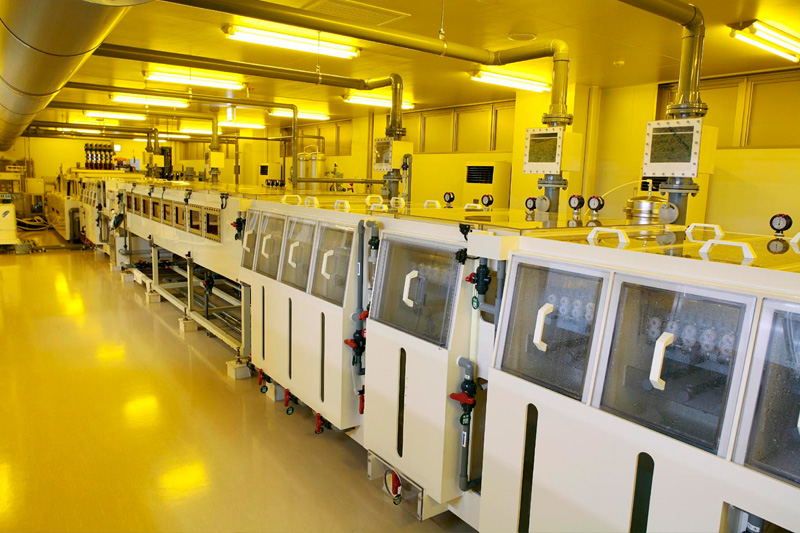
07
AOI(パタ-ン検査)Auto Optical Inspection
形成された配線に不具合がないか設計デ-タを基に自動光学検査を行う工程。
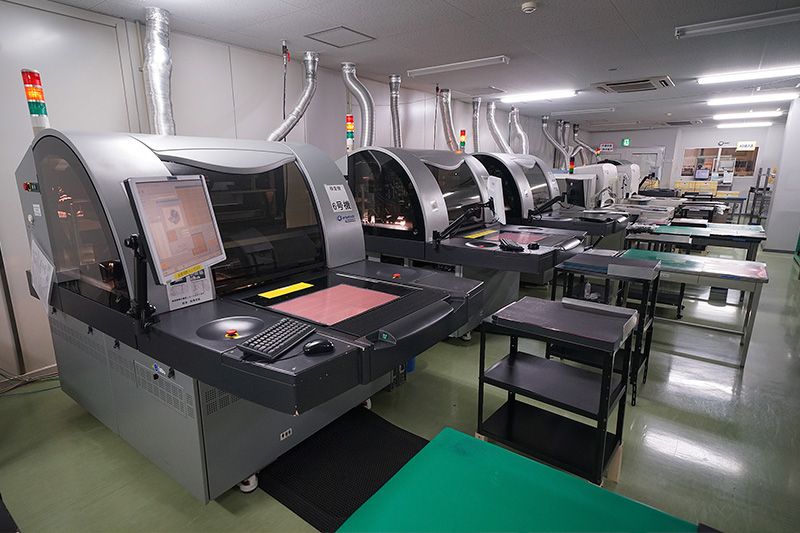
08
前処理(液状レジスト)Preprocessing
配線の保護インク膜を塗布したときに配線と保護インク膜の密着信頼性を確保するための銅表面を粗化する工程。
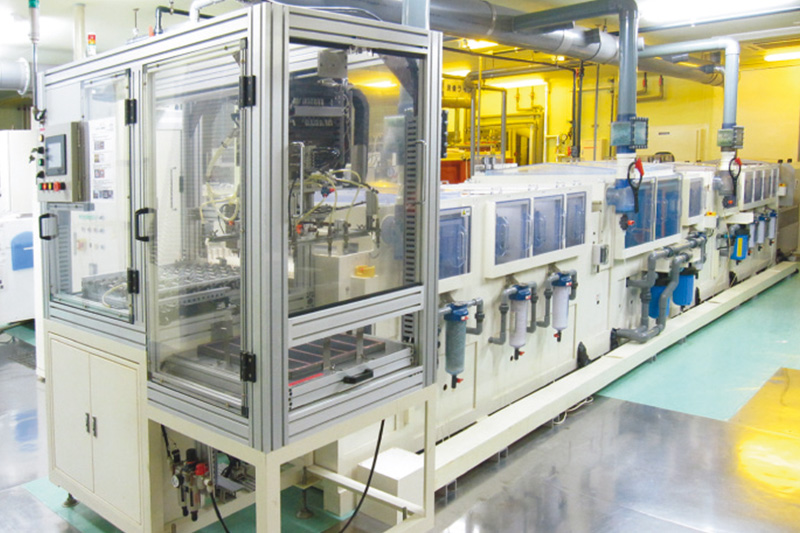
09
インク塗布(液状レジスト)Roll Coater(Liquid resist)
保護膜を形成するために基板表面へ感光性インクを塗布する工程。塗布方法にはロ-ルコ-タ-とスクリ-ン印刷の2種類の塗布方法がある。
(画像:ロールコータ機)
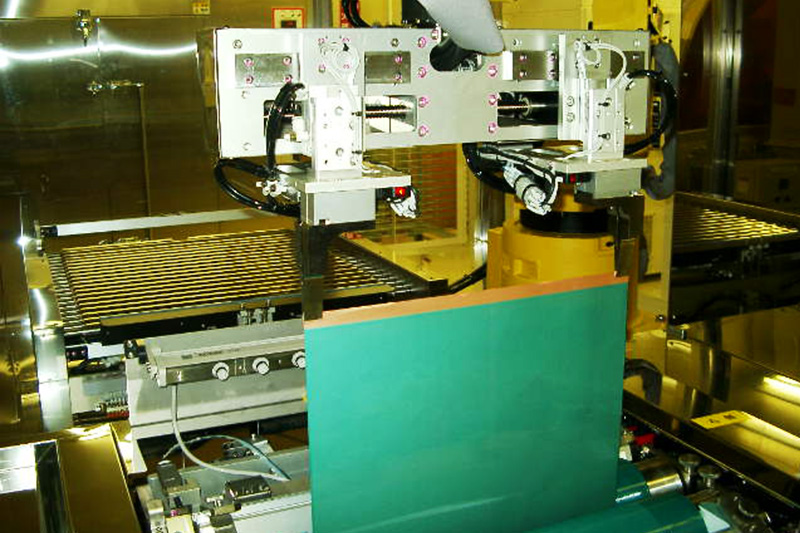
10
露光(液状レジスト)Exposure (Liquid resist)
専用フィルムを用いて保護膜が必要な箇所へ紫外線を照射、保護膜が不要な部分は遮光し照射させない工程。
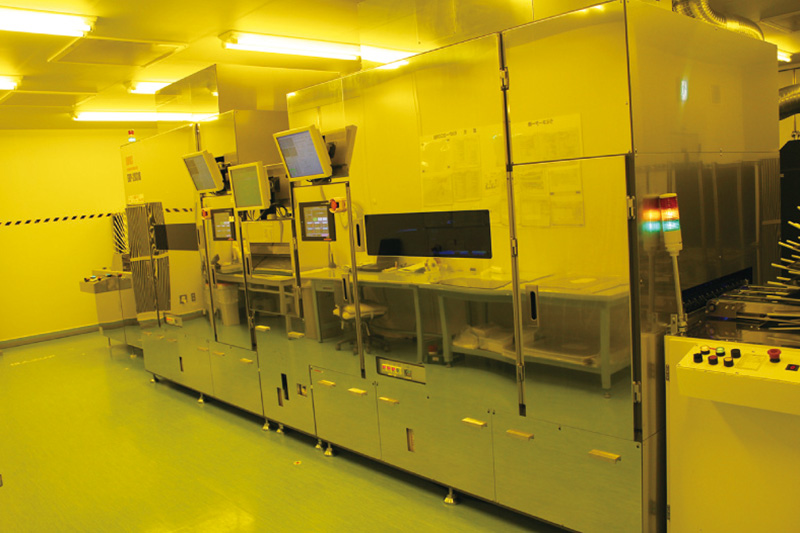
11
現像(液状レジスト)Developing (Liquid resist)
アルカリ性の専用薬液によって金めっきを行う箇所の感光性インクを溶解(除去)する工程。
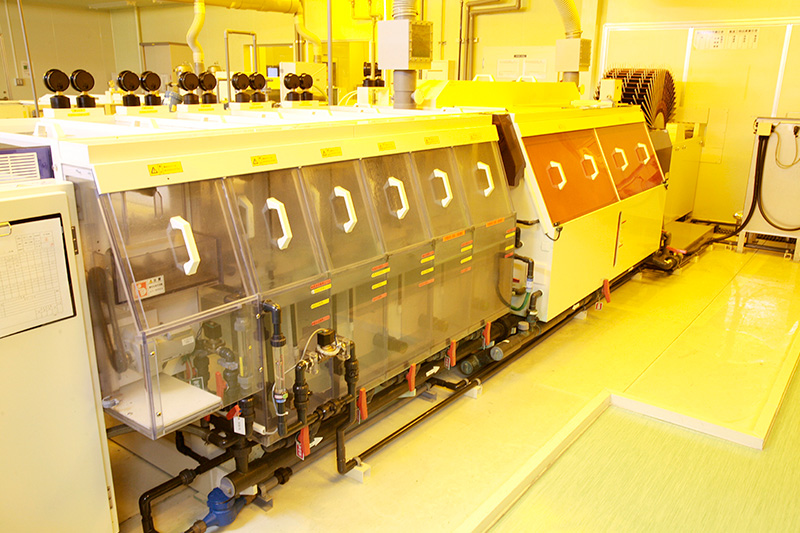
12
金めっきGold plating
ICチップとの接続を行うためにプリント基板のパットや端子部にニッケル・金めっき析出させる表面処理工程。
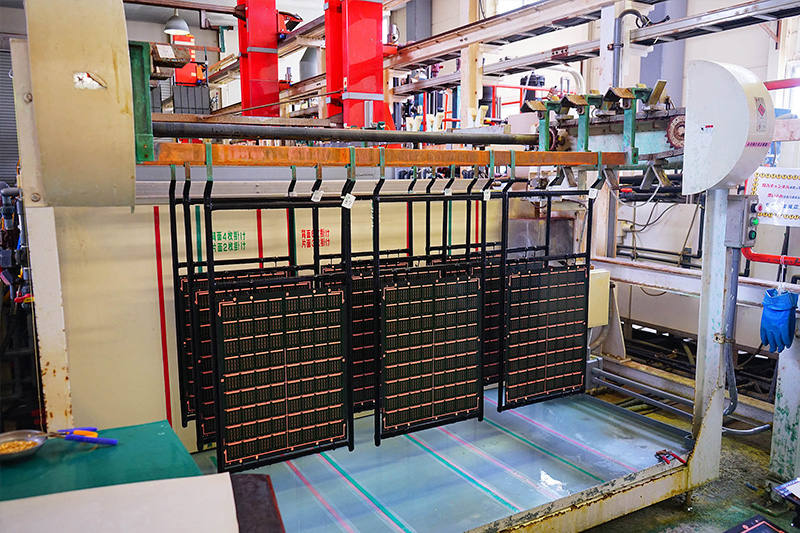
13
外形ルーターExternal router
指定納品サイズになる様、ルータービットを使用し自動加工機でプリント基板の形状を仕上げる工程。
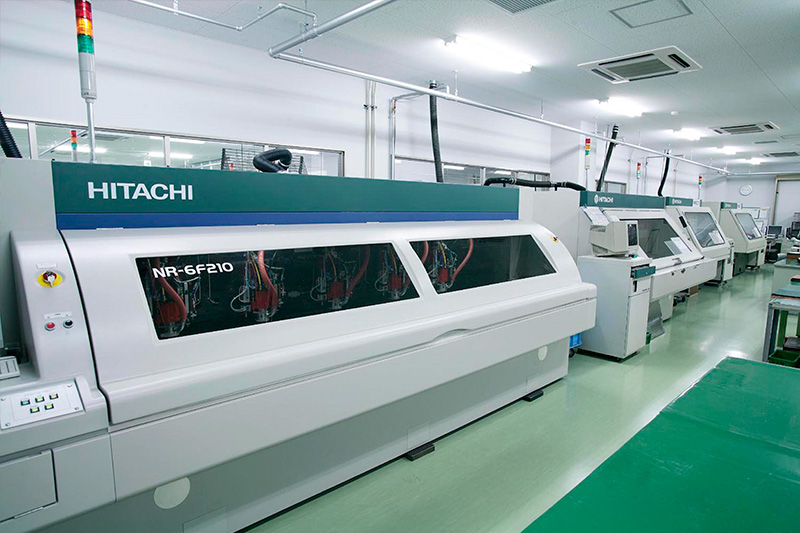
14
仕上げ洗浄Finish cleaning
最終検査前に製品を専用薬品、純水と超音波などを使用し、基板表面の汚れや異物を洗浄する工程。
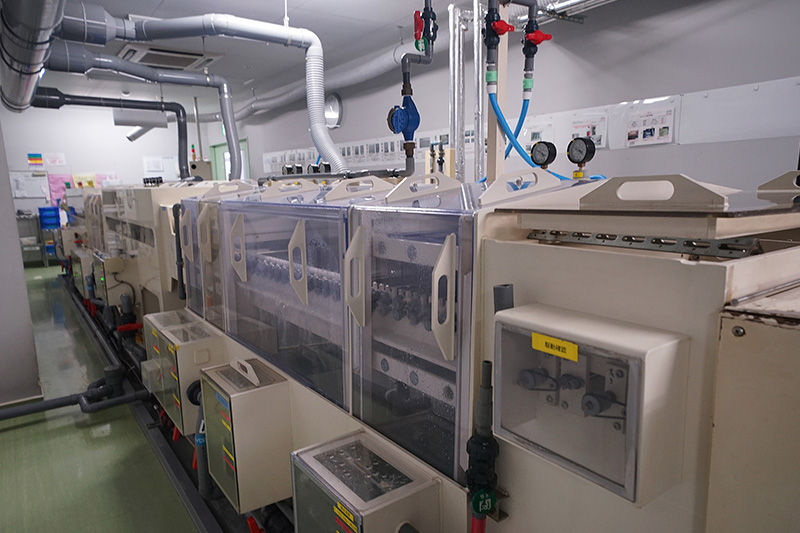
15
AFVI(最終検査)AFVI (Final inspection)
完成品のプリント配線板が不具合無くお客様へ出荷出来るか、最終の自動光学外観検査を行う工程。
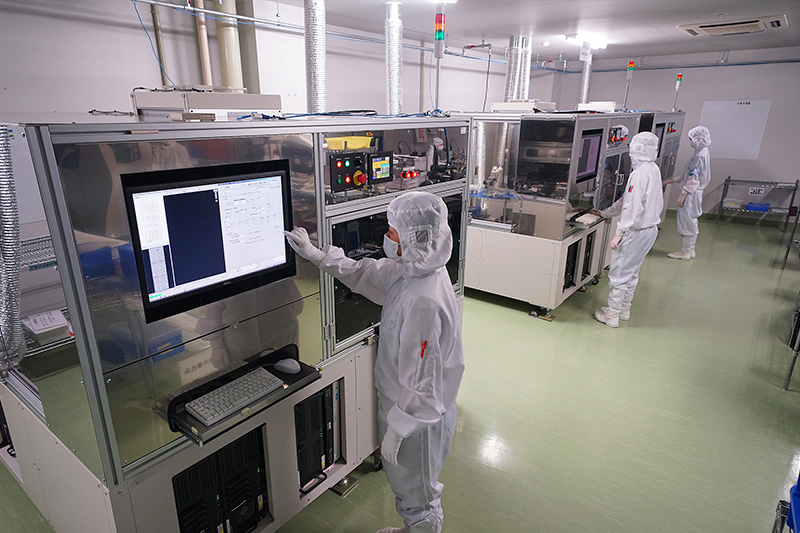
16
レ-ザ-マ-キングLaser marking
プリント基板にレ-ザーを用い、不良品識別や製造履歴追跡用の2次元コードなどを印字する工程。
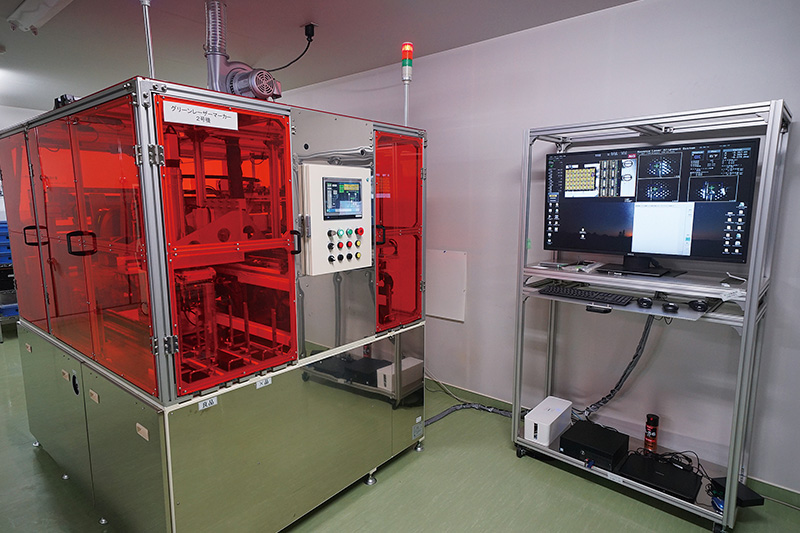
17
出荷保証検査Shipment assurance inspection
お客様の要求規格に適合しているか、信頼性を保っているか、試験や測定を行い出荷判定を行う工程。
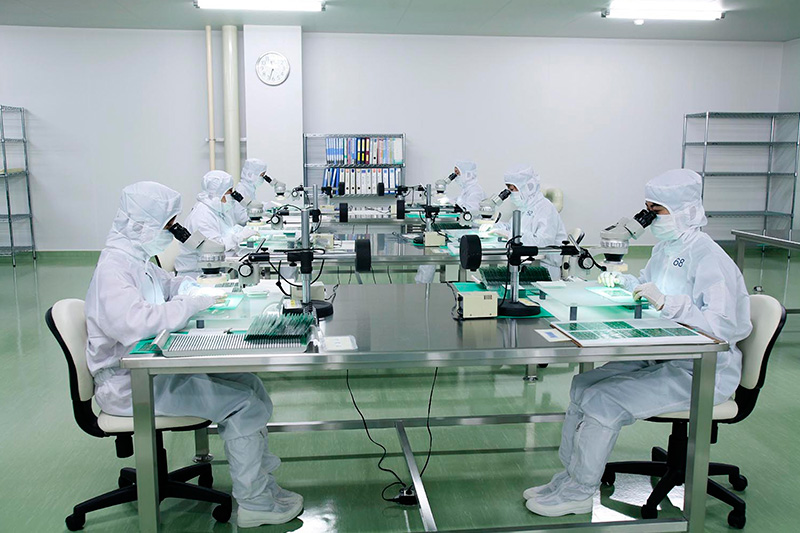